Standard 22 NX
operates accurately and reliably in all environmental conditions
The Standard 22 NX is a gyro compass, a nonmagnetic compass that uses a motor-driven gyroscope to indicate true north. Anschütz designed the Standard 22 NX for high accuracy, reliability and operational safety even under harshest environmental conditions for all kind of ships. With interfaces for serial data, Ethernet and Bridge Alert Management it offers easy installation and integration.
Key Benefits
The upmost in reliability
is offered by Standard 22 NX thanks to its use of unique sensor technology and a robust design that reduces environmental influence (i.e. shocks, vibrations). The high accuracy and reliability of heading information has been proven in over 15 years and more than 20,000 installations.
- Inductive and optical data transmission, no slip rings that are subject to wear
- Unique resistant design reduces environmental influence (i.e. shocks, vibrations)
- Reliability and best accuracy of heading information under any environmental condition, proven many times even in high latitudes
- 24 months warranty for gyrospheres (see GToB)
Service made easy
Standard 22 NX is much easier to install and maintain, and provides multiple interfaces for serial data communication, Ethernet and Bridge Alert Management. Configuration, software update and diagnosis are done via webserver.
- installed by use of standard cabling (redundant CAN bus), less wiring effort
- Webserver functionality for configuration, software update and diagnosis – no need of proprietary tools
- Configuration in 2 minutes possible by upload of a configuration file and more
Secure investment
thanks to a long lifetime of gyrosphere, long maintenance intervals and a long-term stability of heading performance. This way, Standard 22 NX can offer an unsurpassed price-performance ratio over lifetime and thus, best value for money in newbuilding and retrofit projects.
- Unsurpassed price / performance ratio (low initial price)
- Long-term stability of heading performance (rock solid technology)
- Low lifecycle cost because of long maintenance intervals (18-24 months) and long lifetime of gyrosphere
- Approved as gyro compass, gyro compass for high speed craft and rate-of-turn indicator
Type approval & standards
- Compliance to Ethernet data communication according to IEC 61162-450.
- IMO approved: standard and high-speed crafts and as rate-of-turn gyro
- Compliance to Bridge Alert Management (BAM) standards
Main Features
Highest operational safety under harshest environmental conditions.
- High accuracy of 0.4° sec lat rms (in average)
- Integration of up to four sensors, including third-party compasses (up to three gyro compasses, or two gyros and a GNSS THD, and a magnetic compass)
- CAN bus based real time network with up to 400m cable length
- Heading monitor, with manual or automatic switch over of gyro compasses
- Automatic correction of magnetic heading by deviation and variation (with GNSS receiver)
- Quick settling mode
Standard 22 NX interfaces
Standard 22 NX provides heading and rate-of-turn as serial data. Rate-of-turn indicators can be connected directly to Standard 22 NX. All data is also available on two Ethernet interfaces.
The compliance to the Ethernet standard IEC61162-450 ensures that the Radar, ECDIS, etc. can be connected. Standard 22 NX is also compliant to Bridge Alert Management (BAM). A Central Alert Management (CAM) display can be connected via Ethernet or serial data.
Find all technicial data here:
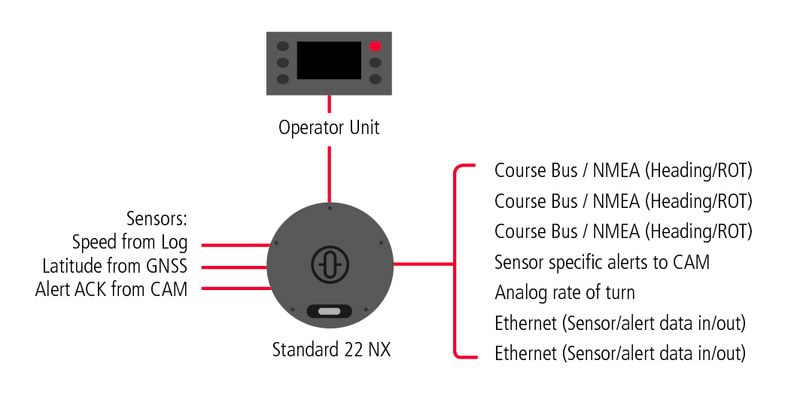
Intelligent system features
Bridge Alert Management (BAM)
Standard 22 NX is compliant to Bridge Alert Management standards. Alerts are prioritized and presented in a consistent manner on the operator unit. Standard 22 NX allows also to transfer the alerts to a Central Alert Management (CAM) display for a central alert presentation on the bridge. Alerts can be acknowledged bidirectional, from the operator unit and the CAM display.
Transmitting magnetic compass (TMC) path
The independent TMC path ensures that a failure in the gyrocompass system does not affect the processing of the magneticheading. With this function, various flag state authorities nolonger require an optical bypass for the magnetic compass onboard of the vessel, resulting in cost savings for the ship yardand the ship owner.
Speed / latitude error correction
Speed and latitude data are provided by sensors or entered manually via the operator unit. The individual speed error correction function ensures that a failure in a log or GPS receiver only affects the heading of one gyro compass. Thus subsequent systems such as dynamic positioning systems are able to detect a heading error caused by an incorrect latitude or speed information at an early stage.
Modular system architecture
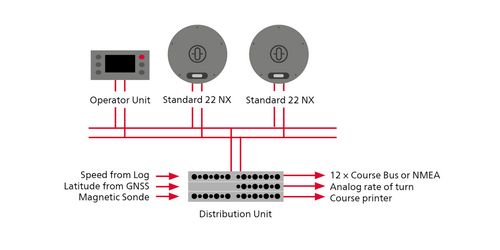
Standard 22 NX heading management system
This system allows to connect up to three gyro compasses and integrates a magnetic compass or GNSS compass. 12 serial outputs are available in addition to the 4 outputs of Standard 22 NX for the connection of heading receivers, such as repeaters, autopilots, radars and others.Sensor selection is done with the operator unit. The threshold for a heading difference between different compasses can be defined by the user and is continuously monitored.Thanks to the CAN bus the wiring effort between the compass components is reduced to a minimum.

Standard 22 NX heading management system with redundancy in distribution
This system provides a redundancy of the distribution system in addition to the redundancy of compasses. No single failure in this configuration causes a loss of heading information to the connected heading receivers. Such a system (with two gyros) is compliant to the demanding class notations such as DNVGL NAUT-OSV/OC/AW, LR IBS or ABS NIBS.